Explore the Simertec All-In-One Method, our answer to the evolution of industrial mechanics.
An advanced approach that integrates various steps, from customs management to shipping and quality control, revolutionizing the procurement of industrial components.
Through the infographic, dive into every step of this journey designed to lower your supply chain costs and give you a unique competitive advantage.
Learn how we combine technology and service to take your projects to the next level.
Welcome to the era of efficiency and excellence.
Simertec All-in-one Method
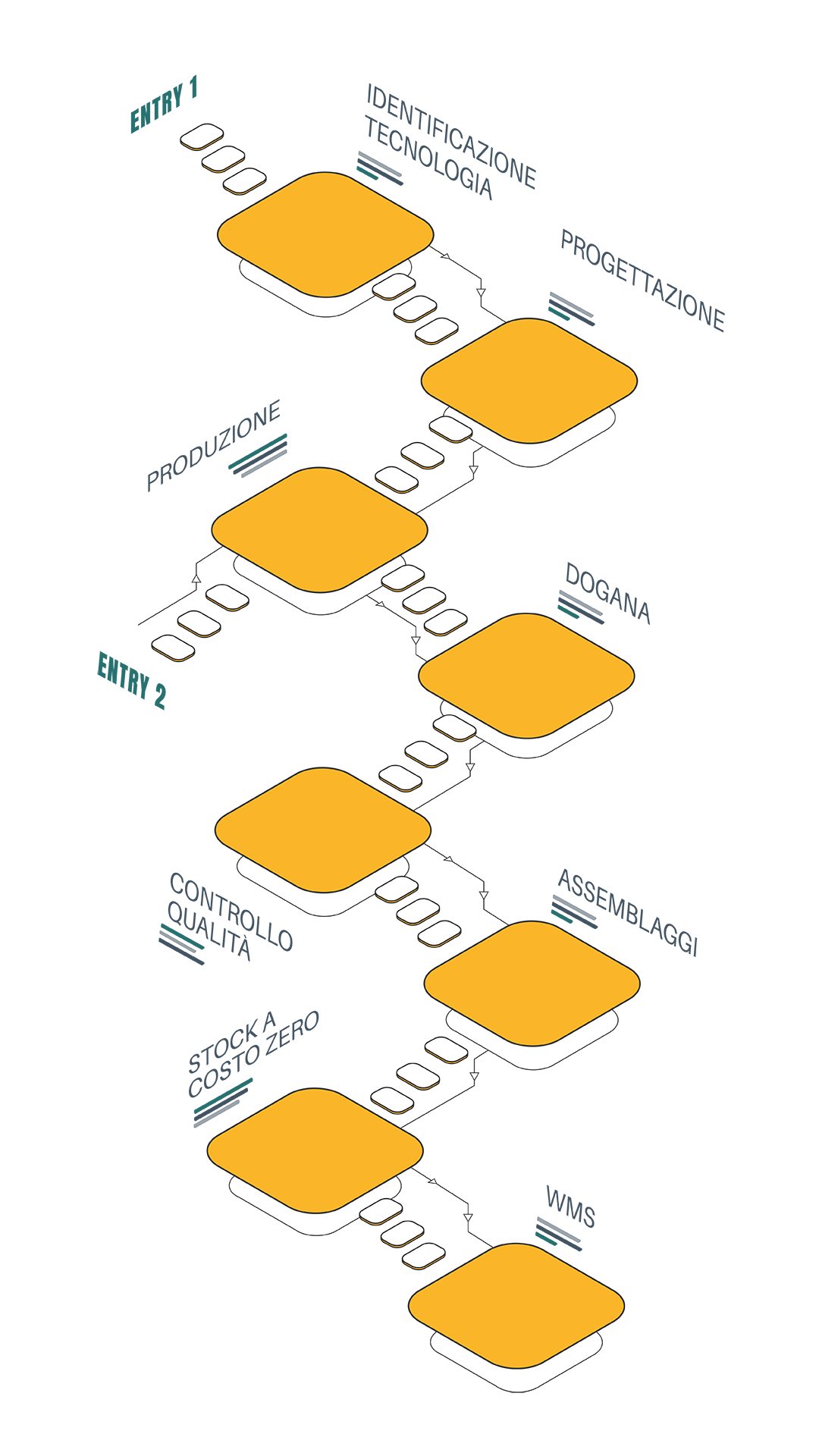
Technology identification
Project analysis involves selecting the most appropriate technology, working closely with the customer and taking into account functional and mechanical requirements.
We find the right balance between production demand and the most cost-effective manufacturing technology to ensure full compliance with requirements.
Design
We are committed to providing comprehensive support based on our expertise.
This includes design development, which may involve modifying existing drawings to make them more suitable for the chosen production process,
or creating new drawings based on samples or detailed specifications.
production
Each drawing code has specific tolerances and requirements to be met to ensure an industrialization process in line with agreed standards.
Simertec benefits from a solid production capacity thanks to the collaboration with several Italian and international partners, with whom we have established solid
and long-lasting relationships over the years.
quality control
Quality is at the core of our operations.
Every component undergoes a rigorous inspection process, with our team using precision instruments to ensure all customer-specified standards and tolerances are flawlessly met.
We conduct a triple-check process to guarantee that each product upholds the highest quality standards.
customs
Simertec’s industry experience and strength have enabled us to achieve T1 Approved Location status in 2022.
This certification allows us to handle the entire import process by sea and air, including customs clearance in cooperation with AEO operators.
At our new location we can directly clear industrialized products abroad, significantly reducing waiting time and avoiding any stopovers.
assemblies
For Simertec All-In-One, delivering a complete service means starting with design and ending with the delivery of ready-to-use components.
When needed, we offer part completion or full machine assembly through our machining and assembly department, even designing dedicated lines for specific projects.
This approach enables our customers to achieve substantial savings in time and logistical space.
ZERO COST STOCK
We manage and store your materials at our facilities at no additional cost, ensuring you always have a reserve on hand and guaranteed supply coverage.
You can take advantage of:
- 17,000 square meters of floor space, 10,000 of which is covered
- 2,800 pallet places extendable to 5,000
- 1 Modula automated warehouse dedicated to sampling
- 900 sqm reception and material preparation area
- 650 sqm assembly and repair area
WMS
A valuable partner like Toyota guided us in implementing an integrated approach to warehouse and production logistics.
We have transformed supply chain complexity into a competitive advantage by simplifying space management, optimizing goods handling, and maximizing resource utilization.
Our achievements include reduced logistics costs, shorter lead times, optimal space utilization, full process digitization, and enhanced service levels.